In this report, we take a close look at the best laser diode sources for automotive lidar.
The laser source is arguably the most important component of any lidar system.
Laser characteristics like wavelength, power, and pulse duration ultimately determine key lidar performance parameters.
These parameters include range, sensitivity, noise immunity, frame rate, and field of view.
As a hobbyist or lidar system design engineer you need to take several factors into account when selecting a laser source for an automotive lidar system.
It is important for you to find the right balance between performance and costs.
Crucially though, the performance requirements for self-driving cars are basically non-negotiable. This is serious business, the penalty for poor performance could be the loss of an expensive car or death.
The aim of this report is to guide you through the main factors you need to consider when choosing a laser source to be integrated into an automotive lidar system.
I will start by looking at the standardization of autonomous driving capabilities.
This should give you a balanced perspective on the performance level needed to achieve true self-driving cars.
From here, I take you through a (shockingly brief) crash course on semiconductor laser diodes.
Next, we discuss two important issues; laser source operation mode (pulsed or continuous wave) and laser source wavelength.
After doing this, you finally get to learn about my (hopefully awesome) picks for laser diode sources for automotive lidar.
I make every effort to compare my picks. I conclude on a clear winner for the trophy for best laser diode source for automotive lidar.
At the moment, camera and radar sensors are routinely included in cars.
The plan for the coming years is to integrate lidars into cars and eventually upgrade the automotive user experience.
The holy grail is of course to reach the level where we have cars with full self-driving ability.
In general, lidar measures the distance to objects by bouncing light from a laser source off them and capturing the reflected signal with a sensitive receiver.
You can learn more about how lidars work by checking out our feature report on lidar technology.
You will only relinquish control of your car if it becomes abundantly clear that it can use instruments like automotive lidar sensor modules to make much better decisions than you.
In order to achieve this automotive lidar systems need to:
- accurately measure the position and velocity of different types of “objects of interest”,
- distinguish between pedestrians, other cars, road signs (possibly with help from cameras),
- work hitch-free in varying adverse weather conditions (heat, rain, smog, snow, etc.),
- and measure ranges over a wide array of distances – from a few meters to hundreds of meters.
The 6 levels of autonomous driving
In order to better understand the self-driving ability of cars, it is useful to look at the six levels of autonomous driving defined by the Society of Automotive Engineers (SAE).
These levels are defined as follows;
- Level 0: No Automation.
- Level 1: Driver Assistance.
- Level 2: Partial Automation.
- Level 3: Conditional Automation.
- Level 4: High Automation.
- Level 5: Full Automation.
Most commercially manufactured cars sold to the public today fall in level 2 or level 3 of the SAE autonomous driving classification.
There have been some cases of lidar included in these level 2/level 3 cars, but this is not widespread.
Levels 4 and 5 of autonomous driving is already available through fully self-drivable services like Waymo.
Waymo’s self-driving cars (see the example in the pic below) comprise a conventional car augmented with specialized lidar hardware collecting raw data which is then fed to machine learning models.
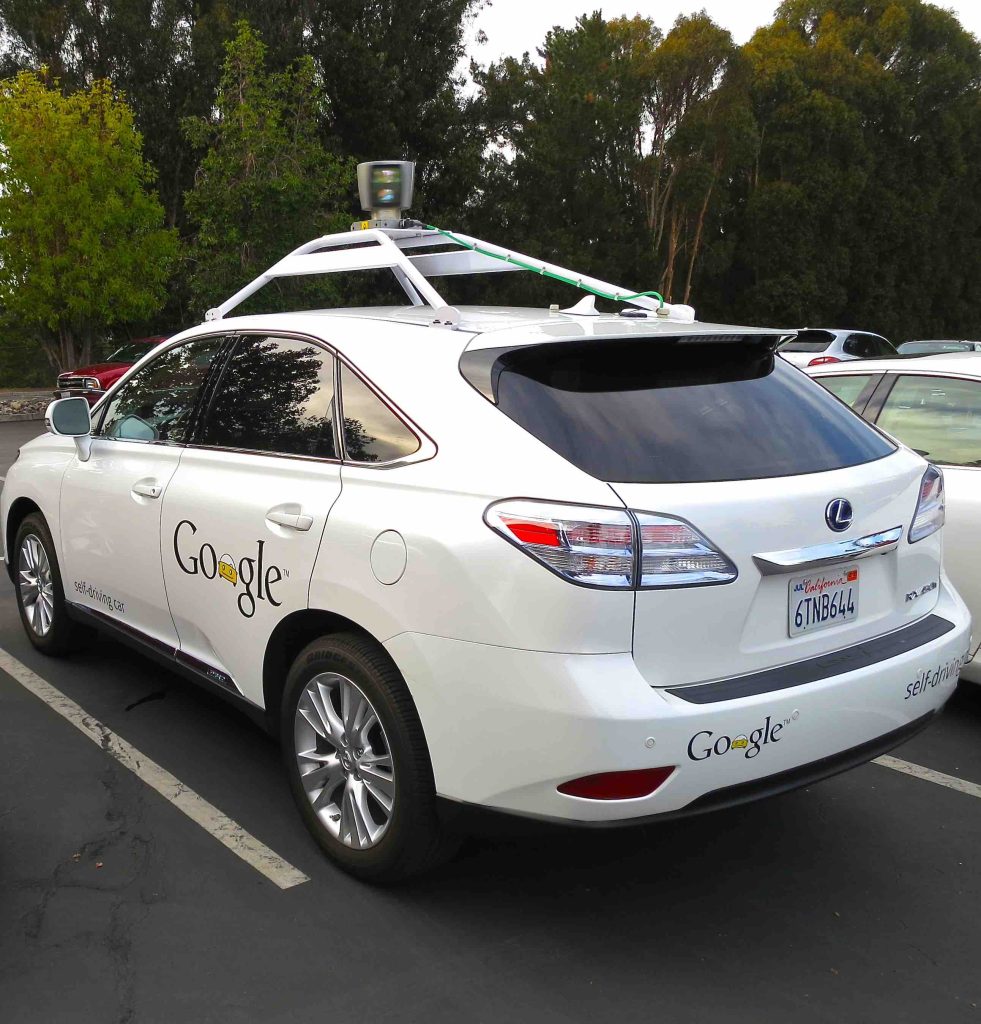
Lidar systems with capabilities far beyond what we have today would be critical to realizing such cars.
There are several challenges that need to be tackled by automotive lidar sensors to make level 4/level 5 autonomous vehicles real.
Even though lidar performance parameters like range, resolution, frame rate, field of view, and cost are affected
Lidar sensor range
Self-driving cars require a sufficient lidar range in order to function properly.
A self-driving car should be able to detect and classify objects located at various distances from it.
Detection of objects close to the car is not that challenging.
There are many lidar sensors that can detect objects located at distances ranging from a few meters up to a few tens of meters.
The real challenge lies in detecting objects located far off from the car.
The braking distance of a car traveling at typical highway speeds (120 km/h or 72 mph) determines the acceptable upper limit of the lidar sensor range.
The braking distance and safety margins mean the range requirement for automotive lidar sensors is upwards of 500 meters.
This ensures the car’s onboard computer has sufficient time to make the appropriate decision to guarantee the safety of the car’s occupants and pedestrians alike.
This is a key attribute for any future self-driving vehicle.
The laser used in the lidar sensor module needs to be powerful enough.
It should emit a sufficiently strong beam so a reasonable amount of photons get reflected from far-off objects.
The laser beam propagates through air. Bad weather and other stray light sources may interfere with it and deteriorate the range of the lidar module.
However, the laser source should not be so powerful that exposure to its beam poses a safety risk for people.
The eye and skin safety of passengers (in other cars) and pedestrians are of primary concern.
The safe laser power level is dependent on the maximum permissible exposure for the wavelength of light that is used.
In particular, the laser beam is eye-safe if it is rated a class 1 i.e. its emitted power never exceeds the maximum permissible exposure for the operating wavelength.
The maximum permissible exposure is the upper limit on the power of the laser source used in the automotive lidar module.
Similarly, there is a lower limit on the power of the laser source. This is determined by the laser source photon budget at the lidar receiver.
The photon budget is the number of photons entering the lidar module’s photodetector after emission from the laser source, and reflection off an object at a given distance.
Ideally, you need to have a sufficient number of photons left over to ensure the photodetector can reliably detect objects.
This means the photon budget scales roughly proportionally with the range of the lidar module.
The photon budget is higher for objects close to the lidar module and decreases as you move further away. At a certain distance, it degrades to a level where reliable detection of objects becomes impossible.
To conclude this section, you should “take home” the message that automotive lidar modules need to use the appropriate class 1 type of laser. This makes it possible to achieve high performance without compromising lidar eye safety.
Other lidar module features like resolution, frame rate, field of view, and cost also depend on the type of laser source used.
However, given the central importance of lidar range, I will not deal with them in detail here.
Crash course on semiconductor laser diodes
So far, you have learned about the levels of self-driving ability. Now, we turn our focus to the basics of semiconductor laser diodes.
The laser was discovered over 60 years ago and has been thoroughly researched since. Today there are several types of lasers used in different fields of technology.
These include solid-state lasers, gas lasers, liquid (dye) lasers, and semiconductor lasers (also known as laser diodes).
What type of laser is used for automotive lidar?
Among the different types of lasers listed above, laser diodes are the light source of choice for automotive lidar.
Laser diodes are ideal sources for automotive lidar because they are compact, energy-efficient, relatively immune to temperature variations, and allow for precise electrical control of their emission.
Laser diodes are well suited for integration with electronics, beam shaping optics, and other mechanical parts necessary to construct a functional lidar unit.
As their name implies, these are special diodes with a gain region sandwiched between p-type and n-type semiconductor materials.
The gain region of a laser diode is made out of intrinsic semiconductor material where electrons and holes can recombine to produce photons.
Laser diodes are heterostructure devices i.e. different materials grown together as if they were one crystal.
The p-type and n-type layers have electrical contacts. These electrical contacts are used for forward-biasing the “p-i-n” junction.
This causes holes and electrons to flow from the p-type and n-type semiconductors respectively into the intrinsic region.
The “p-i-n” heterostructure on its own is not enough to have laser action. In order to get a laser, an optical cavity or resonator is needed.
This is usually created by cleaving both edges of the p-i-n heterostructure to create highly reflective surfaces.
Fabry-Pérot (FP), distributed Bragg reflector (DBR), and distributed feedback (DFB) laser diodes
Recombination of electrons and holes generates photons that are confined in the intrinsic/gain region.
The photons propagate in the gain region in the longitudinal direction.
They make several passes through the gain region as they bounce off the reflective facets of the cavity.
Such a cavity is called a Fabry-Pérot cavity. Hence, these lasers are also commonly called Fabry-Pérot (FP) laser diodes.
There are other ways to create the optical cavity necessary for laser action.
For example, one of the cleaved facets mentioned above can be replaced by a high index contrast, highly reflective Bragg mirror to form a distributed Bragg reflector (DBR) laser diode.
Another possibility involves creating a low index contrast, and low reflection diffraction grating close to the p-i-n heterostructure. This enables accurate control of the emission wavelength of the laser. This is the distributed feedback (DFB) laser diode.
All the laser diodes mentioned so far are edge-emitting i.e. you have laser emission from the cleaved edge of the wafer.
The light beam coming out of an edge-emitting laser diode is astigmatic.
It has a distorted (often elliptical) shape with a high divergence.
It is wider in the vertical direction (~ 30o off the perpendicular) than in the horizontal direction (~ 10o off the perpendicular).
It is often necessary to use a lens to fix this astigmatism and obtain a uniform/useful beam shape with a single focal point.
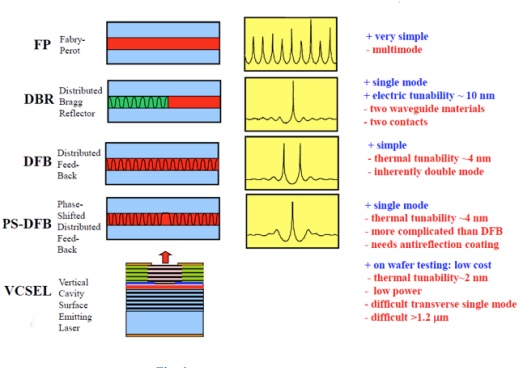
Vertical cavity surface emitting laser (VCSELs) diodes
Interestingly, there is yet another type of laser diode with an advantageous geometry.
This is the vertical cavity surface-emitting laser (VCSEL).
VCSELs are formed by epitaxial growth of DBRs above and below a gain region.
This ensures light travels in a vertical cavity and exits the laser in a direction perpendicular to the surface of the wafer (as opposed to its cleaved edge).
In contrast to edge-emitting laser diodes, VCSELs have many desirable properties for lidar:
- They emit from the top of the wafer. This means they can be tested early on in the manufacturing process. Consequently, their manufacturing throughput can be much higher (compared to edge-emitting laser diodes) and hence costs can be reduced to a minimum.
- Their working mechanism and structure mean they are easily configured into two-dimensional VCSEL arrays which are very attractive for lidar.
- The light beam emitted by a VCSEL is circular with a much lower divergence than that of an edge-emitting laser diode. The optics required to shape the outgoing beam doesn’t need to be so complex i.e. reduced cost.
Consequently, we can conclude that even though edge-emitting laser diodes are more commonly available, VCSELs offer better performance for a lower cost and open up better possibilities for (integrated) automotive lidar devices.
Pulsed vs continuous wave laser diodes for automotive lidar?
After learning about the different types of laser diodes, it is time to look at the mode of operation of laser sources used in automotive lidar modules.
Laser diodes can work in either pulsed or continuous wave mode. Lidars that use pulsed laser sources are called time of flight (ToF) lidars.
On the other hand, frequency modulated continuous wave (FMCW) lidar uses a continuous wave laser source.
As their name implies, ToF lidars measure distances to objects by timing a light pulse as it travels from the laser, reflects off the object, and then falls on a photodetector.
In contrast, FMCW lidars can calculate the position and velocity of an object in a single measurement by determining the frequency shift between a reference signal and the signal reflected from the object.
FMCW lidar is inherently better than ToF lidar.
It has high immunity to stray light (e.g. from other lidars or solar glare) since it filters out signals which are not coherent with its reference signal.
For automotive lidar systems, there is no margin for error.
A car traveling at high speed should be able to precisely detect pedestrians, animals, or other cars and react appropriately to guarantee passenger safety.
ToF lidar sensors alone are not enough to achieve this critical goal.
They use cheap lasers but are not very accurate and usually have a low range.
For example, there are many examples of laser diodes that can operate in either continuous wave or pulsed mode.
On the other hand, FMCW lidar requires a laser source with excellent emission properties and a long coherence length in order to obtain a long-range at the requisite accuracy.
Consequently, FMCW lidar requires laser sources which are more expensive than that used in ToF lidar.
FMCW lidar also needs extra electronics to work accurately.
This adds to the overall system cost and can make highly performant FMCW lidar rather expensive.
The high unit cost of top-performing automotive FMCW lidar sensors is a major issue hampering their adoption in the automotive industry.
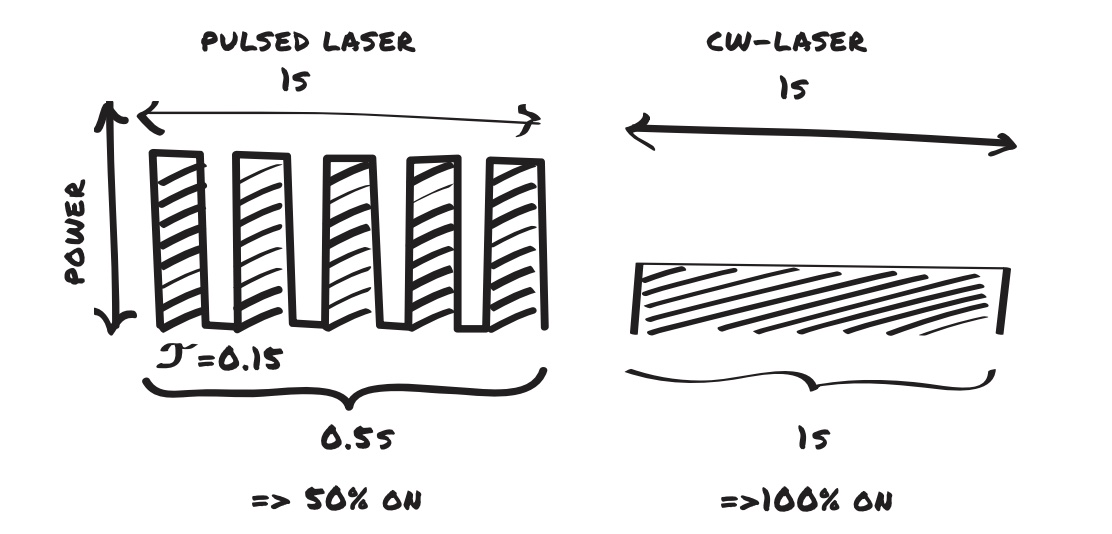
Laser eye safety considerations also come into play when choosing between pulsed and continuous wave lasers for automotive lidar.
Automotive lidar sensors should not harm motorists or pedestrians during their normal operation.
Pulsed lasers are usually rated for the same power level as continuous wave lasers.
This can unfortunately mislead you into thinking pulsed lasers present less risk.
Even though they can have the same average power, a pulsed laser can have far higher peaks than a continuous wave laser.
For example, a 5 Watt continuous wave laser will always output 5 Watts of optical power.
On the other hand, a pulsed laser with the same average power can have peak powers of 250 megawatts. For example, you can have a pulsed laser with 1 picosecond pulse duration. In this case, each of these pulses has 250 microjoules of energy.
Such high peak powers constitute an eye-safety concern as they may exceed the maximum permissible exposure.
This hazard should be taken into account when choosing a pulsed laser source for an automotive lidar system.
What wavelengths are used in automotive lidar?
After learning about the different types of laser diodes, it is time to focus on the operating wavelength of the laser sources used for automotive lidar.
As you are probably aware, most lidars use laser diodes emitting at 905 nm or 1550 nm.
It is only natural then to wonder why these two wavelengths are so popular for lidar.
The choice of the operating wavelength for lidar systems is linked to practical technical factors.
For one thing, lidars can’t use laser diodes emitting in the visible part of the electromagnetic spectrum.
This type of lidar would be too distracting and probably too dangerous given eye-safety concerns.
Infrared wavelengths are a safer bet for lidar laser sources. Their wavelength is outside the visible part of the electromagnetic spectrum.
Additionally, we have many laser diodes with an emission wavelength in the infrared part of the electromagnetic spectrum.
Interestingly, the typical photodetector material responsivity exhibits two main peaks.
One around 905 nm for Silicon photodetectors and another around 1550 nm for Indium Gallium Arsenide photodetectors.
Since lidar systems have to detect weak reflected signals, it is very important to use a wavelength for which the photodetector responsivity is at its best.
Hence, you can understand why 905 nm and 1550 nm are the wavelengths of choice for lidar.
There are some pros and cons related to the use of either wavelength. You can find more information about this in our feature article on the best wavelength for automotive lidar.
Examples of laser diode sources suitable for automotive lidar
Now we have laid some solid foundations, it is time for you to learn about my picks for the best laser diode sources for automotive lidar.
Right now, we are still a long way off from a cheap, compact, and accurate lidar. Automotive lidar modules with the performance necessary for proper self-driving cars simply do not exist.
There is still a lot of R&D needed to get to the point where we have cheap and compact automotive lidar modules with superior performance.
905 nm laser diode source for automotive lidar
Early automotive lidar systems used 905 nm pulsed laser diode sources. ToF lidar is still the most common type of lidar used in the automotive sector.
Consequently, in this section, I will only consider pulsed laser diode sources.
Osram SPL PL90 pulsed 905 nm laser diode (25 W peak power)
The Osram SPL PL90 pulsed 905 nm laser diode is an excellent low-cost option for automotive lidar and collision avoidance applications.
Its pulse duration can be varied from 1 nanosecond to 100 nanoseconds. It emits a beam with a duty cycle of 0.1 percent.
As is typical for this type of laser diode, the output beam is elliptical with a beam divergence of nine degrees (horizontal) and 25 degrees (vertical).
To evaluate performance metrics for integration into a lidar module, we consider the maximum permissible exposure and photon budget for this 905 nm laser diode with a pulse duration of 100 nanoseconds.
If you think back to a few sections ago, we encountered the maximum permissible exposure earlier.
The maximum permissible exposure for a 10-second exposure to an SPL PL90 laser diode with 100 nanosecond pulse duration is 13 milliwatts per square centimeter.
For this laser diode with a peak power of 25 Watts, the power reaching the photodetector after reflecting off an object (assuming 10 percent reflectivity) located 100 meters away is only 11.3 nanowatts.
For the same object located 300 meters away, the power reaching the photodetector is only 1 nanowatt. This is 11 times less power for a distance multiplied by three.
For a 100 nanosecond pulse duration, the number of photons emitted by the SPL PL90 905 nm laser diode is roughly 11.4 trillion.
Looking at the photon budget also gives an interesting outlook.
For the object located 100 meters from the laser diode source, the number of photons received at the photodetector is only five thousand.
For the object located 300 meters from the laser diode source, the number of photons received at the photodetector is roughly 450.
These numbers give you an idea of how weak the reflections can be. Using a pulsed laser diode with a higher peak power can help with improving these numbers.
1550 nm laser diode source for automotive lidar
1550 nm is the most important wavelength for long-haul fiber optic telecom applications. It is also used extensively for integrated photonics.
1550 nm will be the wavelength of choice for future integrated photonic lidar chips. While waiting for the time when high-performance photonic lidar chips, you can already use 1550 nm laser diodes for time of flight (ToF) and frequency modulated continuous wave (FMCW) lidar.
In what follows, I give one example each of 1550 nm laser diodes suitable for time of flight and frequency modulated continuous wave lidar.
TO56-103-116 1550 nm pulsed Fabry-Pérot laser diode (24 W peak power)
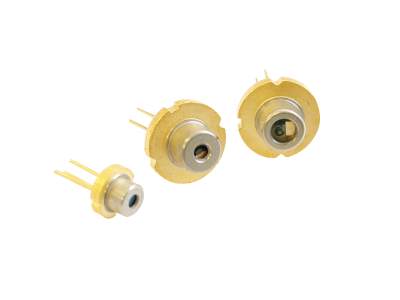
The TO56-103-116 is a 1550 nm Fabry-Pérot laser diode that can function in pulsed or continuous wave mode. When operated in pulsed mode, it has a peak power of 24 Watts with a pulse duration of 150 nanoseconds and a duty cycle on 0.1%.
To compare this with the SPL PL90 905 nm pulsed laser diode, you need to consider the MPE and photon budget.
The MPE for the TO56-103-116 is 0.1 Watts per square centimeter. Compared to the SPL PL90, the TO56-103-116 has an MPE that is eight times higher. This is a significant lidar safety win for the 1550 nm pulsed laser diode.
For reflection off an object located 100 meters from the laser diode source, up to 12.7 thousand photons are received at the photodetector.
When the TO56-103-116 operates in pulsed mode with a peak power of 24 Watts and pulse duration of 150 nanoseconds, it emits about 28.1 trillion photons. The power reaching the photodetector after reflecting off an object (assuming 10 percent reflectivity) located 100 meters away is only 10.9 nanowatts.
For reflection off the same object located 300 meters from the laser diode source, the number of photons received at the photodetector is roughly 1200.
This is a significant gain (3 times more) in photon budget compared to the SPL PL90.
The TO56-103-116 can also operate in continuous wave mode. In this case, its average power is rated at 24 milliwatts.
The TO56-103-116 1550 nm laser diode is definitely superior to the SPL PL90 905 nm laser diode when used for automotive lidar.
The only point counting against it is its cost which is several times higher than the 905 nm laser.
This high cost makes it challenging to integrate the TO56-103-116 into a cheap automotive lidar module.
Conclusion
In this report, I introduced you to laser diode sources suitable for automotive lidar.
I started out by looking at the performance level which is required of current and future automotive lidar systems.
Next, I ran you through a crash course on laser diodes.
This was followed by a review of important aspects which need to be considered when choosing a laser diode source for integration into an automotive lidar module.
In the end, I presented two choices for laser diodes suitable for use in automotive lidar modules. One 905 nm laser diode and one 1550 nm laser diode.
This report focused on discrete laser diode sources for automotive lidar. As I explained earlier, the future of automotive lidar will be made possible by integrated photonic chips.
These are at the moment experimental (sub) systems that are still being built by various companies around the world. Notable examples include companies like Sense Photonics, Velodyne Lidar, Leddartech, etc.
In a future report, I will dig deeper into the innovative work these companies are doing to bring you the latest updates from the front lines of lidar technology.