Have you ever wondered why all automotive lidar systems use laser diodes emitting at either 905 nm or 1550 nm? In this report, you will learn why this is the case.
Oh and even more interesting, you will finally get to learn which wavelength is best for automotive lidar.
The question we focus on in this report is an important one since advanced automotive lidar is a key component in future self-driving cars. As you probably already know, lidar stands for light detection and ranging. It is a remote sensing technique that uses a laser light source to map out its environment.
Automotive lidar systems overwhelmingly favor using laser diodes. Laser diodes are great for automotive lidar since they are cheap, have a small form factor, and high quantum efficiency.
The working principle of an automotive lidar module is pretty simple.
The distance to objects can be estimated by comparing their “time of flight” (ToF) i.e. the time it takes for light to travel from the laser source, bounce off an object, and hit the photodetector.
ToF lidar systems were used in the earliest versions of automotive lidar.
Alternatively, it is also possible to have automotive lidar modules using continuous wave lasers.
These are known as frequency modulated continuous wave (FMCW) lidar systems. FMCW lidar allows for an object’s velocity and distance to be extracted in a single measurement.
This is achieved by coherently mixing light reflected from objects with a reference local oscillator. You can learn more about this by checking out our report on lidar technology.
Why do lidar systems use infrared light?
It is evident that a lidar’s peculiar working mechanism imposes limits on its operating wavelength.
The choice of key lidar components like the laser source, photodetector, electronics, etc. is restricted by practical technical concerns.
The photodetector is the one element that selects the operating wavelength of a lidar module.
The wavelength window where the photodetector’s efficiency peaks is the optimal lidar operating wavelength.
If you think about it for a moment, it makes sense.
Advanced automotive lidar requires the detection of signals reflected by objects located at distances ranging from 300 meters to 500 meters away from the vehicle.
At these distances, the signals reflected off objects of interest can be pretty weak.
What’s more, some objects have a rather low reflectivity. In some cases, this reflectivity can be as low as 10% or 20%.
Consequently, in order to maximize the chance of reliable object detection, the lidar operating wavelength should match the wavelength where the photodetector’s efficiency reaches its peak.
The most common (read cost-efficient) semiconductor photodetectors are either Silicon-based, Germanium-based, or III-V based e.g. Indium Gallium Arsenide (InGaAs).
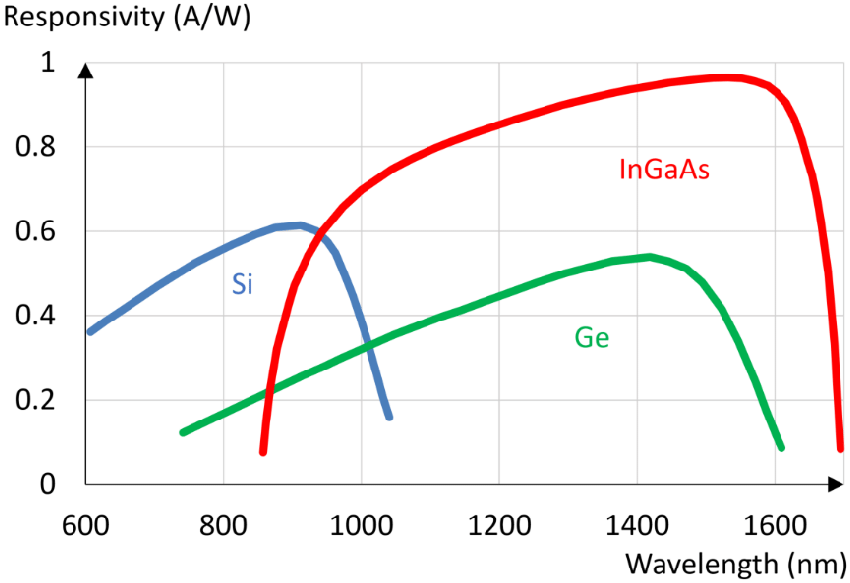
The figure above shows the typical photodetector material responsivity as a function of the wavelength.
Silicon photodetectors have a responsivity peaking at about 900 nm while InGaAs photodetectors peak in responsivity at about 1550 nm.
Germanium photodetectors can also be used but they have lower responsivity with a peak around 1400 nm.
In more practical terms though, silicon photodetectors are widely used because they are cheap (silicon is abundant on earth).
After silicon photodetectors, InGaAs photodetectors are widely used since they have higher responsivity.
Germanium photodetectors are mainly used for custom projects (no mass production) since they are not that responsive compared to the other two types.
Now that we have the wavelength of the photodetector figured out, we turn our attention to the laser diode source.
It has to emit at wavelengths coinciding with the maxima in photodetector responsivity.
The laser diode source must emit a beam with enough power to travel far enough, reflect off an object, and retain enough power to be detected at the photodetector.
However, care must be taken to make sure the laser is not so powerful that it becomes a safety hazard for the eyes or skin of passengers in other cars or pedestrians.
We will revisit this concern later on in this report.
Popular laser diode wavelengths for automotive lidar – the 3 telecom wavelength windows
Commercially available laser diodes cover a wide range of wavelengths in the ultraviolet (UV), visible, and infrared (IR) parts of the electromagnetic (EM) spectrum.
As we learned in the previous section, the choice of the laser operating wavelength for automotive lidar is dependent on the photodetector.
At this point, a small history lesson on the development of optical fiber telecommunication systems should help us move forward with our quest.
Over 50 years ago, Robert Maurer, Donald Keck, and Peter Schultz (all working at Corning Corporation) developed a 29-meter-long piece of optical fiber with attenuation of only 17 dB/km.
An attenuation of 20 dB/km had been understood to be the limit where fiber optic information transmission would become viable. Needless to say, this discovery paved the way for more R&D in this area.
Today commercial optical fibers used for long-haul optical telecommunications have losses as low as 0,2 dB/km.
Attenuation as mentioned here is a measure of the amount of light lost between the input and output of an optical fiber. It is measured in decibels per kilometer (dB/km).
For light propagating in an optical fiber, attenuation is wavelength-dependent i.e. for certain wavelengths, it is minimal.
It is only natural then that engineers designed fiber optic telecommunication systems with transmitters operating at wavelengths matching these minima in attenuation.
In the figure below, you can see a plot (not to scale) of the attenuation in an optical fiber vs wavelength has 3 minima. These are the so-called telecom transmission windows.
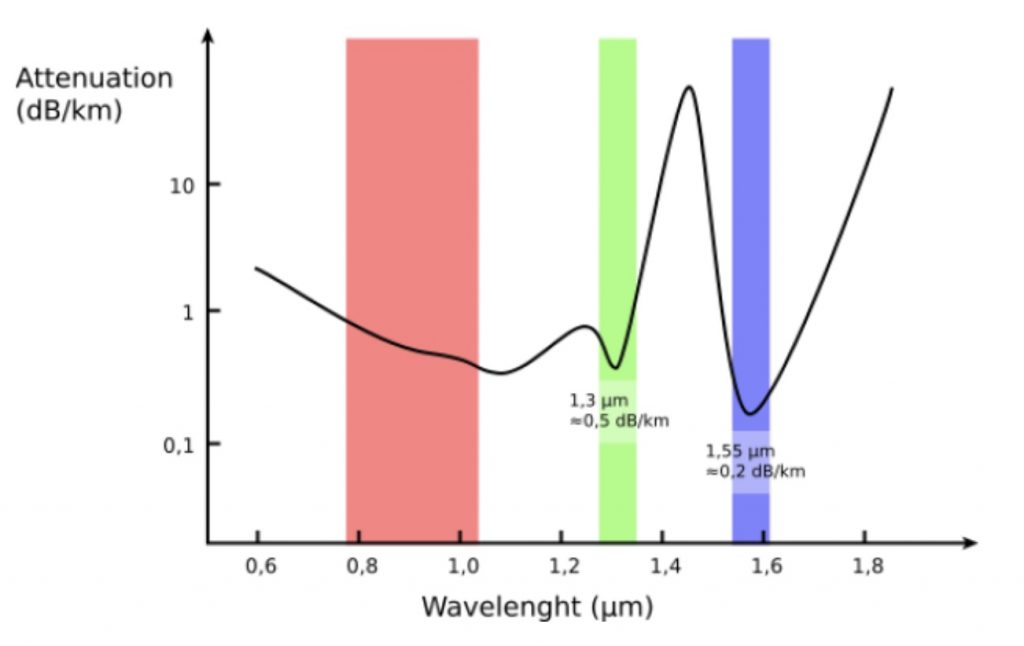
The three telecom transmission windows are centered around 900 nm, 1300 nm, and 1550 nm. The transmission window around 900 nm was the first one to be used.
Initially, light emitting diodes (LEDs) were used as transmitters together with silicon photodetectors. The LEDs were later on replaced with laser diodes.
This first transmission window has a higher attenuation than the other two. It is mainly used for short-distance communication and frequently employs cheap plastic optical fibers.
The 1300 nm window is attractive because, in addition to low attenuation, it also has minimal dispersion.
On the other hand, the 1550 nm window is very popular since it corresponds to the wavelength where very efficient erbium-doped fiber amplifiers are available.
The 1500 nm window is ideal for long-haul fiber optic telecommunication systems.
Automotive lidar wavelength: 905 nm or 1550 nm?
If you put the previous sections of this report together, you immediately get why automotive lidar modules either use 905 nm or 1550 nm. On the one hand, you have 905 nm.
905 nm lidar combines cheap silicon photodetectors with reasonable responsivity with relatively cheap 905 nm laser diodes. They are used extensively in other applications like industrial manufacturing, robotics, and sensing.
On the other hand, you have 1550 nm with high peak responsivity photodetectors coupled with 1550 nm laser diode or fiber laser sources. These are usually more expensive than their 905 nm counterparts.
Given these two main lidar wavelengths, it is natural to wonder which one is better. There is considerable debate and rather conflicting conclusions on this matter.
In what follows, I lay out all the facts for you and follow this up with a conclusion.
Two reasons why 905 nm lidar is better than 1550 nm lidar
We start out by looking at the reasons why 905 nm lidar modules may be better than 1550 nm lidars.
In particular, I draw your attention to two aspects where 905 nm lidar is better than 1550 nm lidar.
1550 nm lidar is more expensive
1550 nm laser diode sources and detectors are typically more expensive than their 905 nm counterparts. Photodetectors for 905 nm light are made out of silicon.
Silicon is a relatively abundant material meaning these photodetectors are cheap.
1550 nm laser diode sources and photodetectors are based on compound III-V semiconductor materials.
These are alloys made from elements from groups three (III) and five (V) in the periodic table of elements.
Examples include Indium Phosphide and Indium Gallium Arsenide. These compound semiconductors require complex manufacturing processes.
Hence, these laser diodes and photodetectors are more expensive.
In the automotive business, cost control is king. One of the issues hampering the widespread adoption of lidar modules in cars is their cost.
Understandably then, cheaper lidar modules using 905 nm are very attractive.
905 nm lidar is more weatherproof
1550 nm light is not as weatherproof as 905 nm light. Automotive lidar needs to operate in a variety of unfriendly weather conditions.
Fog, rain, snow, and wet surfaces all adversely affect 1550 nm signals a lot more than 905 nm signals.
As per a recent report by Velodyne lidar, water absorbs 1550 nm light about 145x more than 905 nm light. Also, Rain and fog degrade 1550 nm light 4x to 5x more than 905 nm light.
Finally, 1550 nm light has 97% worse reflection from snow compared to 905 nm light.
Taking these effects cumulatively, we note that in wet conditions, automotive lidar systems using 1550 nm laser diode sources need up to 10x more power than a similar system using 905 nm laser diode sources.
Power consumption can thus be lower for 905 nm lidar compared to 1550 nm lidar. A lidar module with lower power consumption is always more attractive.
This is especially true given we are transitioning to electric vehicles.
Electric vehicles need to manage the power draw on their onboard batteries. Energy-consuming lidar modules are the last thing you want to contend with in electrical vehicles.
Four reasons why 1550 nm lidar is better than 905 nm lidar
After making a case for 905 nm automotive lidar, we now take a look at the advantages of 1550 nm lidar.
As we have seen so far, using 1550 nm light for automotive lidar has some drawbacks. 1550 nm light is less weatherproof, more power hungry, and has more expensive components than 905 nm light.
Despite these drawbacks, 1550 nm light has some serious advantages; which by far outweigh its disadvantages.
905 nm Lidar is not eye-safe
If you followed our report on lidar eye safety, you can understand that the 1550 nm wavelength is inherently eye-safe. 1550 nm light has a much higher maximum permissible exposure (MPE) than 905 nm light.
To understand this better, we take a look at the example from this article on a 1550 nm triple junction laser diode source for automotive lidar.
According to the IEC 60825, a typical 90 Watt 905 nm laser diode source with a 3 nanosecond pulse width at 100 kHz repetition rate and a 200 um exit aperture has an MPE of 92 nanojoules.
On the other hand, a 1550 nm laser with a 10 nanosecond pulse width at a 400 kHz repetition rate has an MPE as high as 29 microjoules. This is up to 300x higher than what is allowed for the 905 nm laser.
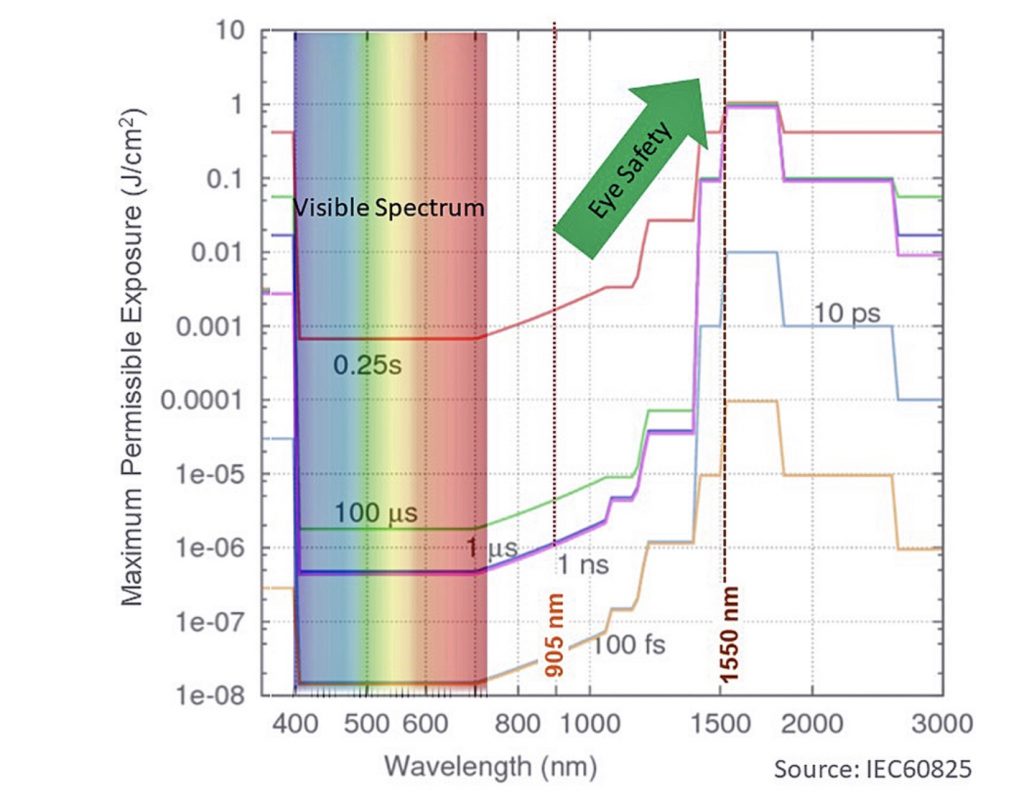
To further drive this point home, consider the plot above that shows the maximum permissible exposure for 905 nm and 1550 nm light for various pulse durations.
As you can see, 1550 nm light has an MPE which is 2 to 3 orders of magnitude higher than 905 nm light.
1550 nm lidar has a better sensitivity
1550 nm photodetectors have a higher responsivity that 905 nm photodetectors. Coupled with this, higher MPE means a 1550 nm lidar module can use more power without harming your eyes.
With more photons available, the signal-to-noise ratio and detection probability for 1550 nm is a lot better than 905 nm light.
This remains true even if we take into account the poorer performance of 1550 nm light in bad weather.
Being able to use higher-powered laser diodes at 1550 nm is a big deal since it makes it possible to have automotive lidar to have long range.
Other factors: solar background noise & integrated photonics
Automotive lidar systems operate out in the open. Atmospheric background solar radiation can negatively impact laser signals emitted by lidars.
FMCW lidar operating at 1550 nm reduces this significantly by only detecting reflected signals which are coherent with the local oscillator.
Most 905 nm lidar modules are time of flight sensors. ToF lidar is adversely affected by solar background radiation. This effectively limits its accuracy and range.
The automotive lidar module of the future will be an integrated photonic chip with a small form factor and no moving parts.
Integrated photonics is the technology that will make this happen. Integrated photonics is ideally suited to the 1550 nm wavelength window.
Examples of such integrated photonic lidar chips already exist. They will only get better as more R&D efforts are put into them in the coming years.
What is the best wavelength for automotive lidar
We have looked at both wavelengths commonly used for lidar and we are now ready to draw a conclusion:
1550 nm light is the best wavelength for automotive lidar – It is eye-safe, has a better range, sensitivity, and signal-to-noise ratio. It is the wavelength of choice for current and future integrated lidar chips with no moving parts.
Lidar modules need to have a reasonable cost in order to ease adoption by the automotive industry. For example, early automotive lidar systems cost up to $ 75,000 dollars.
These were bulky systems using a 905 nm laser source and a photodetector mounted on a rotating platform on the car roof.
Future automotive lidar modules will have a small form factor. This will ensure they can fit into a car’s front grille and only cost a few hundred dollars.
They’ll also have outstanding accuracy over a long range. These are stringent requirements that will ensure they are rather expensive.
Taking a step back, a self-driving car will need several different lidar sensors working together.
More expensive 1550 nm lidar modules can be used for detecting obstacles located up to a few hundred meters ahead or behind the car.
Cheaper 905 nm lidar modules will be focused on sensing the immediate environment of the car.